Low pressure die casting machine for brass
SKU:LPDC
Features
The Low Pressure Die
casting machine are mainly for brass
alloy and zinc alloy metal products, especially on faucets, valve bodies and
sanitary fittings and accessories. To fulfill the different capacity requirement
of customers, we have
1-manipulator and 2-manipulators models for
customer options.
Advanages:
1.
High quality casting and high-precision repeatability , automated casting with
servo motor driving, linear guiding rail system;
2. High capacity ranges 400~450 castings per shift (8hrs);
3.Quick
die change flange, 5 mins by munually ;
4.
Furnace heating method: gas burner is standard and elctricity for option;
5.
Max. die diemension 550*400mm;
6.
Whole set machine cooled by cooling water for a efficiency cooling, highly
improve inductors service life;
7. Zinc Oxide dust cleaning unit for furnace cleaning;
8.
Industrial PC control with Ethernet cables, die casting programs up to 200
saved, recording & tracking furnace
9 .Cost-efficient
production ( reduced melting loss,multiple die,one-man operation,increased yield);
10. Humanization
of the work station (ergonomic design of the work station,minimizing of
heat,noise and danger of accident)
The LPDC5540 equipment
consisting of main components: casting device, induction furnace, receiving
car, graphite bath, die cleaning device,crane, manipulators, hydraulic and
drives system, pneumatic system, riser
tube heating system and control system etc.
The function and
parameters of the touch panel are set by Chinese/ English
1.1.Operation
Control System: With Siemens PLC control device;
1.2 Program Verstions: CN and EN
1.3 Touch screen panel + Team Viewer and
Industrial PC control.
1.4 Alarm and troubles shooting codes
presentation, for problems fixing quickly and maintenance works.
2.1 Manipulator is with
servo motor driving unit, linear guilding rail system, to move the manipulator
in horizontal and vertical direction: faster, more stable and high precision
control performances.
3.1 Induction furance
power is 105KW;
3.2 Large melt content up to 1800kg,
3.3 Melting capacity is 350KG/H,
stepless power adjustment;
3.4 With 3*35KW inductors, each
inductor is water cooling, water flow detection device on water jackets;
3.5 Induction furnace heating methods: standard with gas burner, electricity heating for option ( extra cost)
3.6 Hydraulic opening device
mounted on furnace cover.
3.7 With material
feeding cover and desert cleaning cover, automatically control;
3.8 Furnace Temperature history recording and inspection control progr.
3.9 Furnace opening methods: manually / automatically program
4.1 Receiving car: with performances of moving up-down; forward
& backward;
4.2
Transport the casting products to storage vehicles directly.
Crane with electric
hoist:
5.1
Effective lifting weight 500kg;
5.2 Crane is used
to lift the furnace cover for furnace cleaning, maintenance etc.
Graphite Bath:
6.1
With performances of Constant temperature and graphite agitation.
6.2 With 2 sperated tanks,
tubes and agitators made of stainless steel material( SUS 316L).
6.3 Used for die cooling and coating;
6.4 Graphite coating is for
easier pieces removal and die's temperature control.
6.5 Effective using space: 1124*896mm
Hydraulic and drives
system:
7.1
Components supplies with internationa high quality brands: SUN、REXROTH、YUKEN etc.
7.2 The components
are special used, with performances
of high stability, strong protection
from contamination, suitable for water-based hydraulic oil operation etc.
7.3 The hydraulic
oil ( Ethylene glycol ) works at low
temperature, stable quality, not get deteriorated.
7.4 Servo motor driving, no
vibration.
Furnace casting system:
8.1 The pneumatic components
supplied with NORGREN、FESTO brands;
8.2 Pressure is with proportional
control device;
8.3 With 2- security valves protection design for
guarantee high quality of casting and safety.
9.1 The riser tube on
furance cover are with ceramic sealings;
9.2 Riser Tube heating method: Medium frequency
electricity heating, power 60KW; average power consumption: 7KW;
9.3 Heating time till
900℃ ≈ 90 seconds
9.4 Contains water cooling
system.
10.1 Die Cleaning
Chamber: shot blasting device (copper powder blasting) for the cleaning of the dies.
10.2 The dies can be moved to cleaning chamber automatically for
cleaning process heavy oxidized contaminations condition.
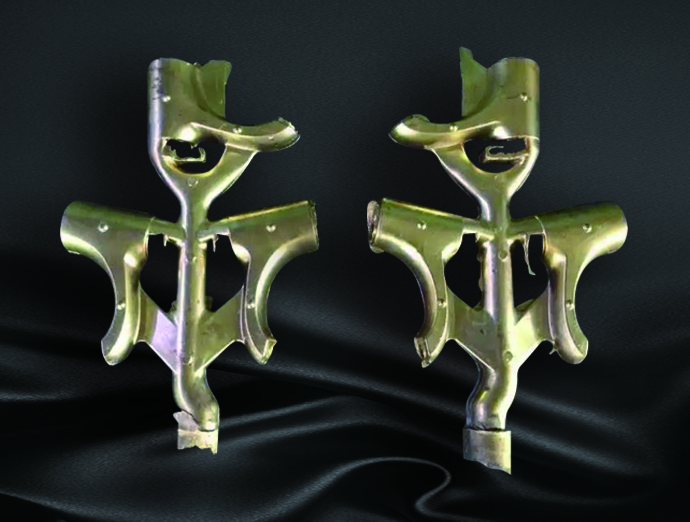